This blog was first published in 2020, and updated in February 2025
In the Elk Valley, mountain-top removal coal mines dig up millions of tonnes of coal every year. When people ask questions about how these coal mines add to climate change, both government and industry are always quick to point out that Elk Valley mines produce steelmaking coal, not the dirty kind of coal that’s burned to generate electricity.
But that misrepresents the problem. Coal is burned in the steelmaking process and nearly all of the carbon in the steelmaking coal ends up in our atmosphere as greenhouse gases. Steelmaking with coal is dirty. Steelmaking is an incredibly carbon-intensive process, responsible for roughly 5.8%1 of global emissions2— 3 times higher than the entire aviation industry3. When we follow Elk Valley coal from the mountains to steel mills, it turns out that its greenhouse gas emissions are more than all of B.C.’s reported emissions combined, including every vehicle, industrial plant, farm and gas facility!
Of course, while we can reduce our use of steel and recycle it, the world is still going to need steel. Fortunately, there are much lower-carbon ways to make steel already in use today and the technology for zero-carbon steel is already here. The reason we keep using coal to make steel, using a process that hasn’t fundamentally changed in more than 100 years, is simple: it’s cheap.
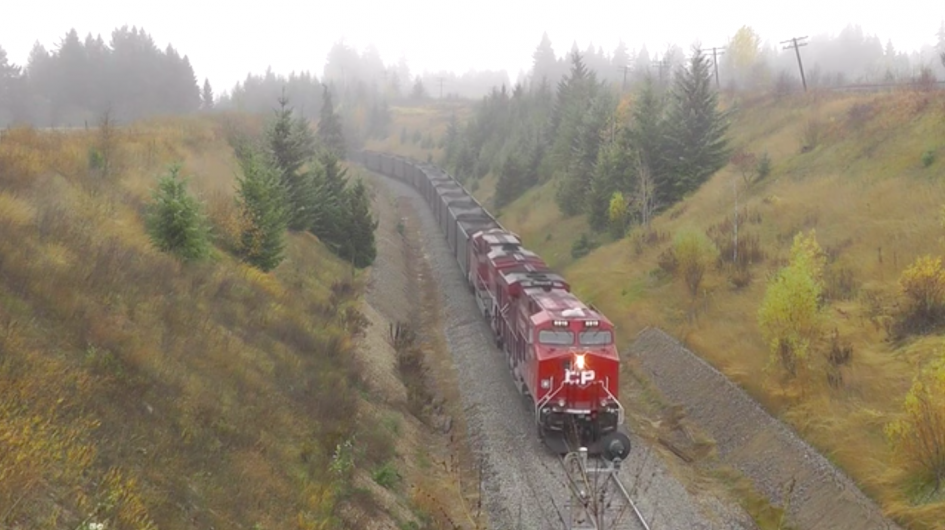
All coal is bad news for our climate
Before we look at the alternatives to steelmaking coal, let’s take a closer look at the Elk Valley coal mines and the steelmaking process. Glencore’s Elk Valley mines are major sources of direct greenhouse gas emissions. Huge amounts of diesel are used to operate heavy equipment and natural gas is used for drying coal. Plus, methane is released from the earth as coal is mined. In total, the mines put out 1.9 million tonnes of greenhouse gases every year4—that’s as much as 650,000 cars and light trucks on our highways5.
In 2024, an estimated 25 million tonnes of coal was shipped out of the Elk Valley—hundreds of train cars every day. From the Elk Valley, the coal travels by rail to the coast and then is loaded onto ships, mostly bound for Asia—and transporting that coal puts out more than a million additional tonnes of greenhouse gases6.
From there, the coal is converted into coke and then used in the blast furnace-basic oxygen steelmaking process. Coal does three things in this process: it is burned to supply the huge amounts of heat required, it supplies gases to strip oxygen from the iron ore and roughly 1% of the coal ends up as carbon in the steel. In the process, about 99% of the carbon in the coal ends up in our atmosphere, adding roughly 67 million tonnes of greenhouse gas per year to our carbon emissions, just from the Elk Valley coal mines7. In total, the coal that starts out underneath the Rocky Mountains in the Elk Valley ends up contributing more to our global climate crisis than the rest of British Columbia combined—that’s more than every car, truck, plane, building, farm, industrial site and gas well in our province8.
Why do we use coal to make steel?
We know that we need to reduce our carbon emissions by 80 or 90% if we want to avoid the worst effects of climate change, so it’s clear that we can’t keep burning coal to make steel. What can we do instead? The good news is that coal is not our only option. You need three things to make steel: a whole lot of heat, some way to remove oxygen to turn iron ore into iron and a little bit of carbon to turn the iron into steel. The carbon is easy, all you need is a little bit and it can come from anywhere: everything from used tires to charcoal to agricultural wastes have been shown to have potential to fill this niche9. To strip the oxygen from your iron ore, hydrogen is a proven option and can be produced from renewable electricity. Heat, which is the bulk of what coal is used for, is the simplest of all and can come from any energy source.
The biggest barrier to carbon-free steel isn’t technological though. It comes down to dollars and cents. Coal is cheap because it’s just dug out of the ground. Renewable energy can be more expensive, but that gap is closing every day. However, coal is only cheap if we ignore the massive costs to the environment and our future when it is burned. If we consider the full cost to ourselves and our planet, renewable energy is without a doubt a lot cheaper than burning coal.
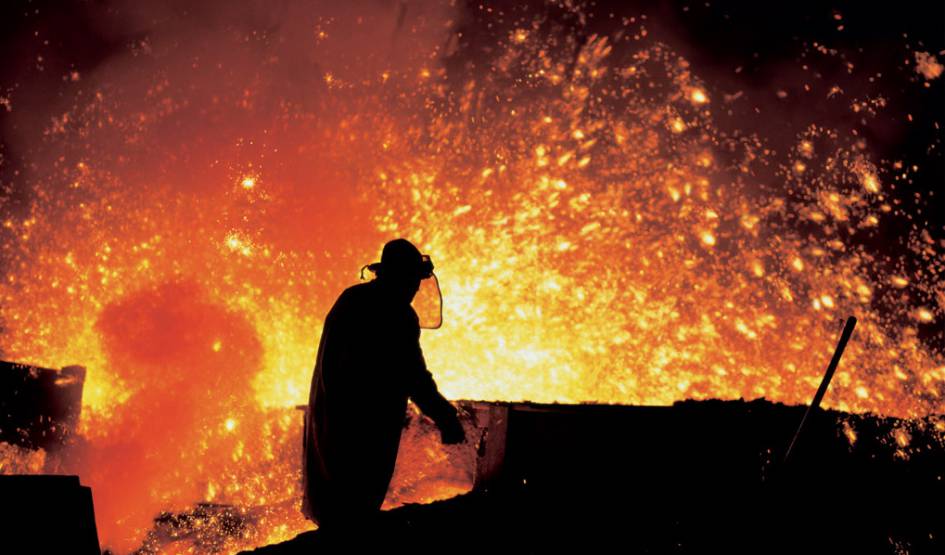
The future of steel
Fortunately, the transition to fossil-free steel production is already underway in many areas, including in Sweden where steel producer SSAB has already delivered hydrogen-based steel to industry on a small scale. Another Swedish company, Stegra, is building a 5 million tonne per year hydrogen-based steel plant, to enter production in 2026. A replacement of SSAB’s smaller blast furnace plant in Sweden with a fossil fuel free steel mill planned for 2028 will slash 10% of the entire nation’s GHG emissions10. It is clear that building greener steel production infrastructure could help to significantly reduce global emissions; governments need to put pressure on the steel industry to move much faster if we are to mitigate the encroaching effects of climate change.
In the meantime, we need to reduce our use of steelmaking coal as much as we can. Fortunately, only 71% of steel is made with coal today11. The other 29% of the world’s steel production uses electric arc furnaces, fed with recycled steel or iron smelted with natural gas and hydrogen. Recycling is obviously a priority to reduce demand for new steel, but most steel already ends up recycled, and recycled steel alone won’t be enough to meet global demand.
But we don’t need coal for the transition to hydrogen-based steel either. There are large industrial plants operating today that use natural gas to produce direct-reduced iron from iron ore, followed by an electric arc furnace to turn that iron into steel. In those plants, natural gas is cracked apart to make hydrogen, which makes up the bulk of the gas used to reduce iron and produce heat. Already these plants have about half the carbon emissions of coal-based steel plants12. It would not be difficult to replace the hydrogen from natural gas used in these plants with hydrogen produced with renewable energy. Using renewable hydrogen together with a small amount of natural gas would drastically reduce the carbon emissions per tonne of steel compared to coal-based steel and would buy us precious time to scale up the world’s production of fossil-fuel-free steel.
If we’re going to get serious about tackling climate change, we’re going to have to get serious about leaving steelmaking coal in the ground. Fortunately, alternatives already exist. Moving away from coal-based steel will be a much easier part of our transition to a low-carbon world than replacing long-haul flights or decarbonizing our farms and ranches.
It’s time to start planning for a post-coal future in the Elk Valley. That means no more new mines or mine expansions, like NWP’s proposed Crown Mountain mine or Glencore’s Fording River Extension, previously known as Castle Expansion. It’s time to stop pretending that steelmaking coal doesn’t have climate consequences and start looking towards the huge task of trying to restore the 150 plus square kilometres of coal mines in the Elk Valley and the heavily polluted waters of the Elk River watershed.
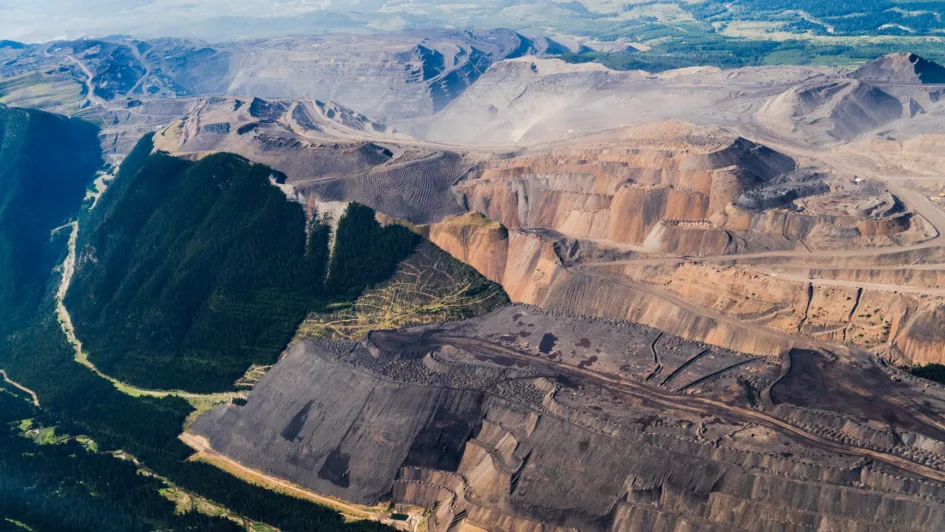
- Emissions measurement and data collection for a net zero steel industry, IEA, April 2023
- Global greenhouse gas emissions, Government of Canada
- Aviation, IEA
- Scope 1, 2 and 3 emissions calculation methodology report, 2022, Teck
- Provincial inventory of greenhouse gas emissions, December 2024, BC government & Light and medium-duty vehicle registrations, Statistics Canada
- Using Canadian National Railway Company figures on carbon emissions per tonne of cargo, per kilometre for rail (~700 km from Elk Valley to Vancouver) and maritime bulk shipping to Asia (~9000 km, roughly the average distance to major coal ports in China, Korea and Japan).
- Scope 1, 2 and 3 emissions calculation methodology report, 2022, Teck
- Trends in greenhouse gas emissions in B.C., Environmental Reporting BC
- Review on the Use of Alternative Carbon Sources in EAF Steelmaking, T. Echterhof, Metals, January 2021
- SSAB receives environmental permit to transform steel plant in Luleå, SSAB, December 2024
- 2024 World Steel in Figures, World Steel Association
- Types of greenhouse gas emissions in the production of cast iron and steel, V G Lisienko et al 2016 IOP Conf. Ser.: Mater. Sci. Eng. 150 012023